In this post we look at more commercial applications
for recovered plastic. Then we look at
what it means for investors who are first to the table in the nascent recycled plastic sector.
On the Road in India
In October 2017,
the Indian government announced a major initiative to building roads across the
country. It appears the roadways in
India are among the least safe in the world so about $11 billion is to be
invested over the next five years to improved as many as 84,000 kilometers of
roadways. One extra mandate from the
federal government - materials made from recycle plastics must be
used.

India has
already had great success with plastic-based road construction materials. The World Economic Forum reports that there
are now 34,000 kilometers of roads in use in India. Developers tout the plastic materials as
environmentally friendly and longer lasting than conventional asphalt. India has to worry about erosion during the
monsoon season. Roads made with a mix of
asphalt and melted water bottles withstand monsoon damage better than asphalt
alone. Perhaps more importantly recycling plastic into road material provides
vital commercial opportunity for the country’s numerous garbage pickers as well
as new jobs running the recycling processes.
India is not
alone in developing plastic road construction materials. The construction services firm VolkerVessels
based in Holland is developing pre-fabricated units that can be transported to
the road site and assembled.
VolkerVessel’s subsidiary KWS has teamed up with the Polymers Business
Unit of Total S.A. for additional development work.
Building Blocks
Construction
bricks are expensive. Worse yet conventional
fired bricks also do not hold up well in earthquake prone regions. Conceptos Plasticos, a
construction company, knows these are obstacles to adequate housing for low
income people in its home country of Columbia.
Conceptos Plasticos has designed a building block made from recycled
plastic. The plastic bricks and pillars
are made through an extrusion process that uses recycled mixed plastics. Additives make the block fire resistant.
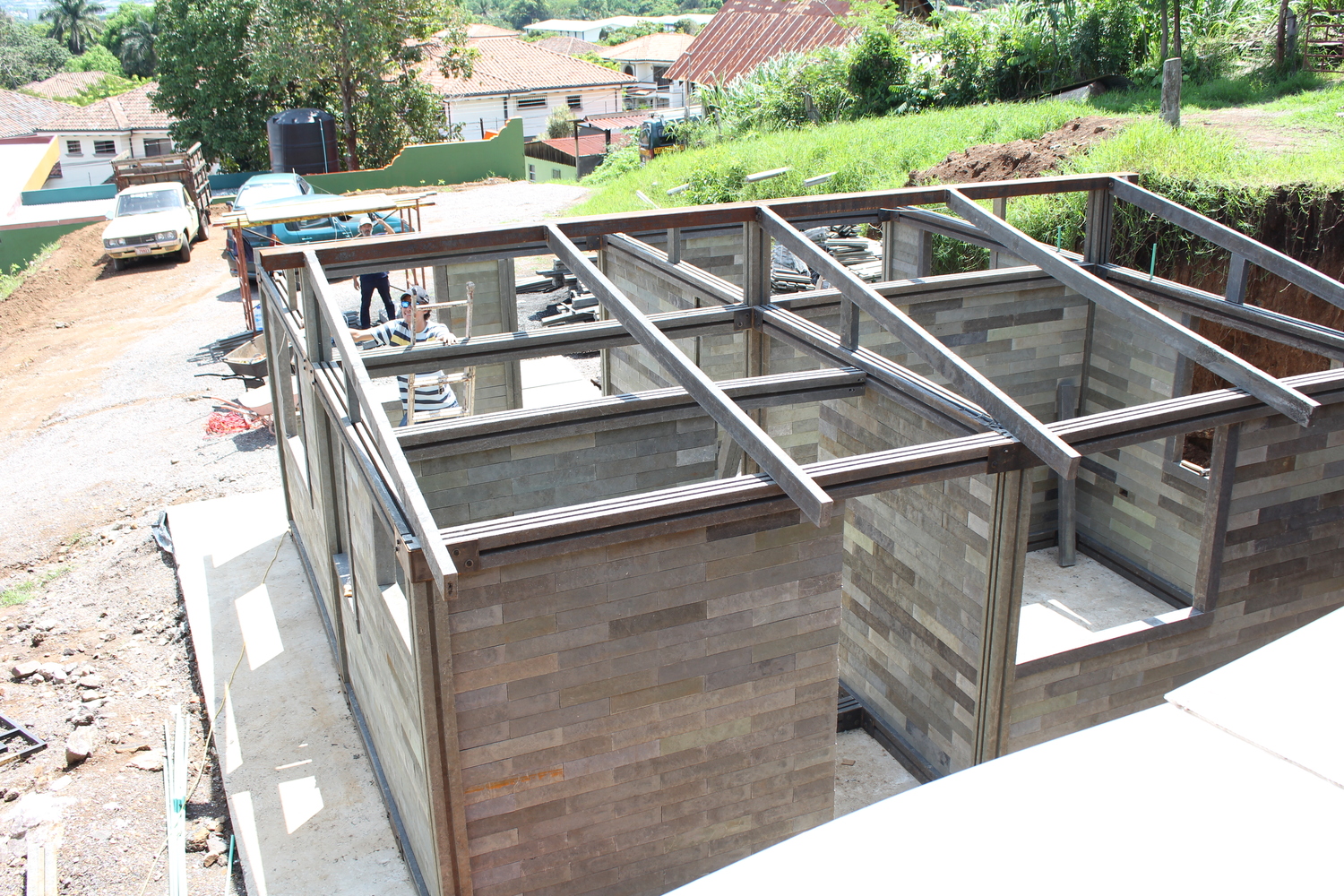
The company claims
its plastic block can save on building costs by 30%. A 40 square meter house
with two bedrooms, a living room, dining room, bathroom and kitchen costs about
US$6,800 (20 million Colombian pesos)
Not only are the blocks less expensive, they
are easy to handle. Homeowners can
construct a modest home with little experience using the patented system of
pre-fabricated bricks and pillars. A
two-story house can be built in two-days.
Conceptos
Publicos has taken in a little over US$300,000 in grants and investments to get
its recycle plastic construction products into the market. Its founder, architect Oscar Mendez, holds
the patents on the construction blocks and system.
New Ideas for Used Materials in Old Products
Investors may
not see the potential for profit-building scale in ideas like plastic bricks
for low-cost housing and alternative materials for roads in less-developed
regions. However, economies of scale could
be built on a foundation of demand from already large industries that accept
recycled plastic components. Dell Technologies
(DVMT: NYSE) has
been involved in recycling for several years beginning with green packaging and shipping practices.
In 2017, the company introduced a plastic laptop tray (the base of your
laptop that holds the electronic circuitry) made exclusively from recycled
plastics, 25% of which is recovered ocean plastic. As a bonus, there is a very cool mother-baby whale duo imprinted on the tray.
Dell is working with Lonely Whale, an ocean advocacy group, on rescuing and intercepting ocean plastics. The key for Dell is establishing a supply chain capable of delivery sufficient quantities on a reliable schedule. To this end Dell and Lonely Whale have launched the NextWave project to bring discarded plastic back to consumers in the form of usable products. Carpet maker Interface, Trek Bicycle and General Motors are three other big names that have signed on with NextWave, bringing big appetites for materials as well as expertise in supply chain development.
Dell is working with Lonely Whale, an ocean advocacy group, on rescuing and intercepting ocean plastics. The key for Dell is establishing a supply chain capable of delivery sufficient quantities on a reliable schedule. To this end Dell and Lonely Whale have launched the NextWave project to bring discarded plastic back to consumers in the form of usable products. Carpet maker Interface, Trek Bicycle and General Motors are three other big names that have signed on with NextWave, bringing big appetites for materials as well as expertise in supply chain development.
Early Stage Precedents
To some
investors recycled plastic may not seem much of an industry. There are a few companies here and there that
are each developing novel repurposed plastic designs. From a ‘glass half-full’ perspective, there
are more companies than there were five years ago. Given social and economic trends favoring
sustainability there are more likely to be even more businesses five years from
now.
The future of recycled
plastic might be predicted by the development of plastic in the first place. Exxon Mobile is among the largest plastic
manufacturers with over $236 billion sales annually, much of it coming from
crude oil development and refining. Dow
Chemical, LyondellBasell, BASF and ENI are also leaders in the plastic industry
with billions in annual sales. The
plastic industry has become the third-largest manufacturing industry in the
U.S. The industry has not always been
so well developed. There was a beginning
stage.
The first synthetic
plastic was commercialized and branded Bakelite by its creator Dr. Leo Baekeland. Polyvinyl chloride, plexiglass, Teflon, ABS
and Styrofoam followed in the next four decades. Each invention brought new players to the
market, all of which moved through the typical business development cycles to
reach scale and profitability.
Dr. Baekeland
founded Bakelite Ltd. in 1909, to produce plastic resins and manufacture
products with moulds and casts. By the
late 1920s Bakelite had acquired three other privately-held plastic
manufacturers. The American Catalin
Corporation got its start manufacturing plastic clock faces using Bakelite
technology that had been acquired by Catalin after the Bakelite patents expired.
Today neither
Bakelite nor Catalin are names that have survived to present day. Mergers and acquisitions over the years have transformed
those names into other brands. In their wake new corporations have sprung up that are more recognizable in today’s plastics industry. A chemist named Wallace Carothers invented
nylon in the late 1930s. The innovation
made it possible for his already highly successful employer DuPont to begin
commercial production of nylon in 1939.
Nylon eventually became one of the Dupont’s most important
products. Given DuPont’s reputation for underpinning
investment decisions on detailed analysis, most likely successes of the early
plastics companies that made the industry look interesting.
It is still not possible
to divine the future any of the recovery and recycling innovators mentioned in this
series on plastics. Will any of them eventually
become the ‘Bakelite’ or ‘Catalin’ precedent of the plastics recycling industry? There is the risk that early stage investors will take.
Neither the author of the Small Cap Strategist web
log, Crystal Equity Research nor its affiliates have a beneficial interest in
the companies mentioned herein.
2 comments:
Thanks for sharing useful information. Keep on sharing.
Plastic producers in Qatar
Plastic companies in Qatar
wow amazing…be sure to check out my giveaway today!.for more information please read plastic bottles in pakistan
Post a Comment